Tool Selection
When making a power tool purchase, the primary factor that should be considered is the application for which the tool is needed. Torque requirements, available space, tool category, and battery size are also important considerations.
Application: Use the right tool for the right job
When choosing a tool, the application requirements need to be fully understood. A tool should only be used under the particular loads and operating conditions for which it was designed, and failure do so may result in reducing its operating life or preventing the tool from functioning entirely. Warranty does not cover tools which have been misused in applications for which they were not designed.
For example, many 3/8" impact wrenches have enough torque to remove car lug nuts, but if they are used in this way the anvils of 3/8" impacts will frequently snap. Warranty does not cover this misuse. 3/8" ratchets can also be used as a breaker bar, but this will either damage the ratchet drive, break internal parts, or spread ratchet towers. All of these conditions will either reduce the rachet's operating life or stop the rachet from working at all.
Accessories
Make sure you are using the correct accessories for your tool and that they are in good working condition.
For example, cracked sanding pads can cause bad vibration both in the tool and on the work surface. Bent arbors and drill bits will obviously not function correctly, and using chrome sockets will cause premature wear on impact anvils.
Further considerations
Cost, weight, ergonomics, size, warranty, and durability are also important considerations when making a tool purchase. We recommend finding as much information as possible regarding these factors to make the best decision.
For example, you may prefer ease of use over other specifications. A smaller, lighter tool may have sufficient torque to remove car tires, but it is not intended to be used for this purpose. If you accept that a smaller tool will fail more frequently in this situation, it may still be an appropriate choice.
Another factor to consider is whether a tool is powered by air (pneumatic) or battery. A pneumatic tool is more durable and will last longer, but a cordless battery powered tool provides greater range without needing an air hose and may possibly provide higher torque. A battery powered tool will inevitably fail more frequently than a similar pneumatic tool with the same use.
Tool ratings
Many tool ratings are sensationalized for marketing and sales purposes and describe tools with terms like "nut busting torque" or "thunder gun." Regardless of the advertised qualities, more practical considerations are much more useful.
For example, the customer should know the CMF and PSI at load rating on the air compressor that will be used with pneumatic tools, and may need to consider a tool's free speed or load RPMs. Drilling 1/2" holes into steel should not be done with a high speed drill (no matter how well it is advertised) because a geared drill with slower RPM is needed to drill larger holes. Sanders and grinders also have a variety of accessories and speeds for different uses, and the more powerful options may not be appropriate.
Impact wrenches
An impact wrench is a power tool designed to produce a high torque output with no effort by the user. The tool accumulates energy by rotating a mass and then delivering the energy (impact) suddenly to the output shaft. Depending on the job, the requirements for torque range, power, and even comfort of use may vary. The impact mechanism's weight, vibration, speed, and durability will change with these requirements.
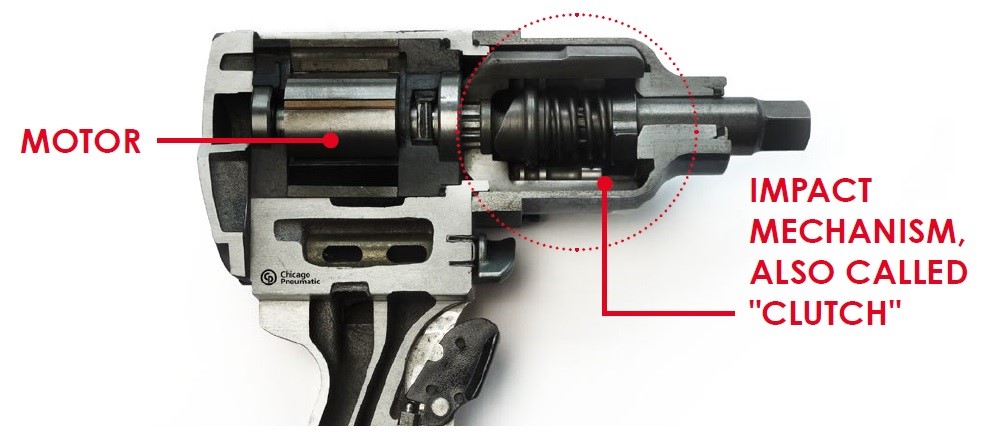
It is very important not to overtighten when using an impact wrench; some applications require precise torque control. For example, when changing the tires on small vehicles or trucks, the torque on the bolts must be set to the manufacturer’s specifications. Using tools with torque limited functions along with a torque wrench will prevent overtightening and causing damag to the studs.
Choosing the right impact wrench will not only ensure maximum performance and comfort, but also the durability of your tool. Remember to check the wrench's specified max torque and working torque, which is defined by an approximate 3.5 second run time, and if the application demands it, also check the specified forward and reverse torque. There are several main types of impact wrench mechanisms used depending on the use case and the type of joint being tightened or loosened. See the diagrams and descriptions below.
Pin clutch impact wrench
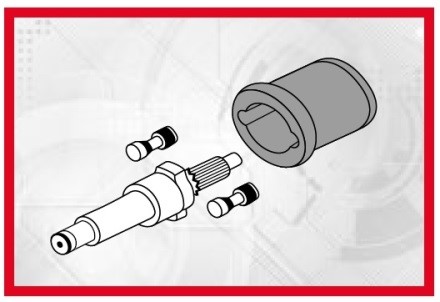
Mechanism: The ball lifts the cam, causing the pins to strike a blow on the anvil. After the blow, the spring returns pins to their starting position.
Use: Excellent on hard joints.
Operation: Extremely low vibration clutch for better operator comfort. Good power/weight ratio.
Single dog impact wrench
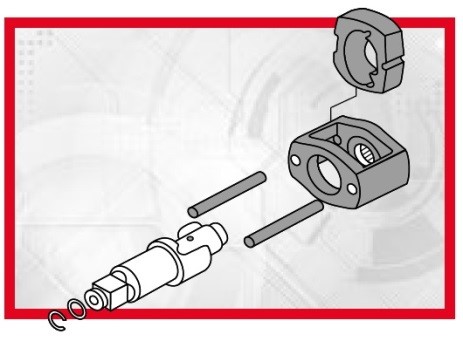
Mechanism: A hammer cage that rotates and drives the hammer to strike a blow on the anvil. The hammer then disengages from the cage and rotates in preparation for the next blow.
Use: Excellent for maintenance and repair operations (MRO).
Operation: Compact clutch. Lighter than the twin hammer version.
Twin hammer/double dog impact wrench
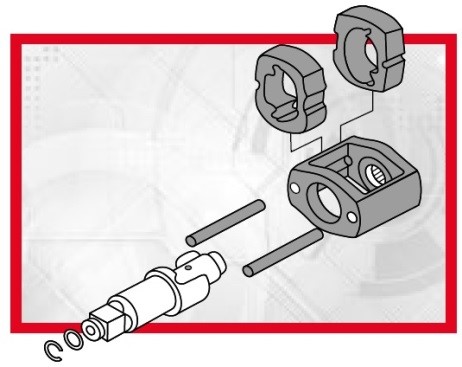
Mechanism: A hammer cage that rotates, driving twin opposite hammers to strike a blow on the anvil. The hammers then disengage from the cage and rotate in preparation for the next blow.
Use: Best choice for light vehicle maintenance. Excellent for hard joints.
Operation: High energy per blow. Very durable, all around clutch. High power/weight ratio.
Rocking dog clutch (pinless or double) impact wrench
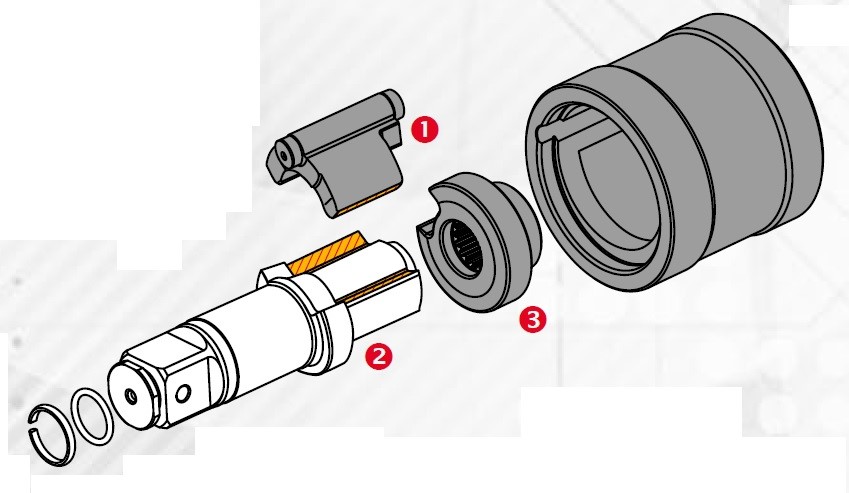
Mechanism: The "dog" (diagram, no. 1) strikes a blow on the anvil (diagram, no. 2). Then the cam (diagram, no. 3) kicks the dog out of engagement and rotates 360° and so the dog can strike again. The impact zone on the anvil is maximum, and ensures an optimum power transmission.
Use: Best choice for heavy vehicle maintenance. Good for soft pull-up jobs.
Operation: High durability. Maxium power. Efficent and well performing with limited air flow because of the heavy cage blow efficiency.
2-Jaw clutch impact wrench
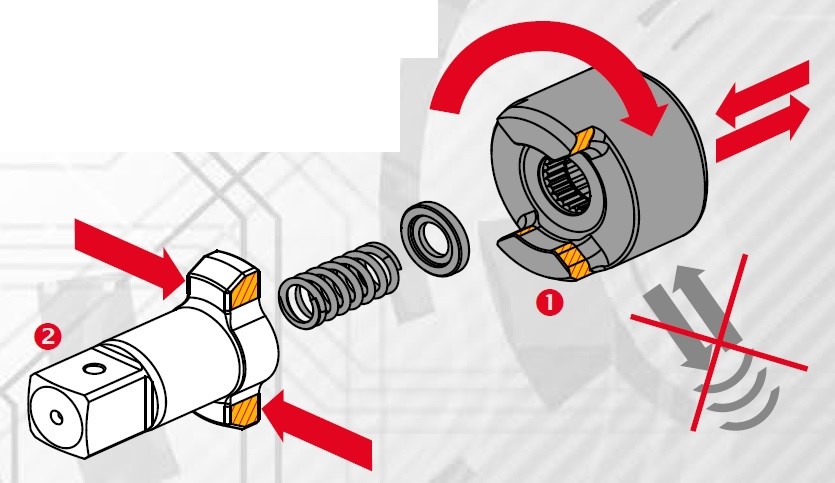
Mechanism: The hammer (diagram, no. 1) hits simultaneously the anvil (diagram, no. 2) on two opposite points for a maximum effect which reduces vibrations.
Use: Best choice for tough duty. Versatile and efficient for all types of joints. High energy per blow and high ultimate torque.
Operation: Comfortable and quiet. Avoids lateral vibrations due to the hammer's round, closed, and symmetrical shape.
Single hammer impact wrench
Mechanism: The single hammer mechanism provides 1 blow per revolution.
Use: Recommended for medium to heavy duty use. Mechanism results in greater hitting power.
Operation: Easy maintenance. Long operating life.
Double hammer impact wrench
Mechanism: Similar to the single hammer, except with 2 counterbalanced hammers that hit twice per revolution.
Operation: Mechanism results in less vibration and operator fatigue that the single hammer.
Hard and soft joints
Soft or hard joints define the nature of the join between two or more surfaces.
Soft joint
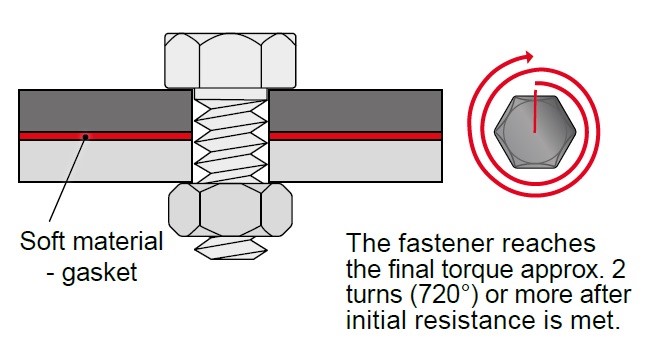
A soft joint has has low resistance when turning the bolt or nut until it reaches its seating, after which resistance slowly increases. A soft joint occurs where the material between the nut and bolt has a low stiffness when subjected to compression by the bolt load. Often the placement of a gasket in a joint results in a soft joint.
Hard joint
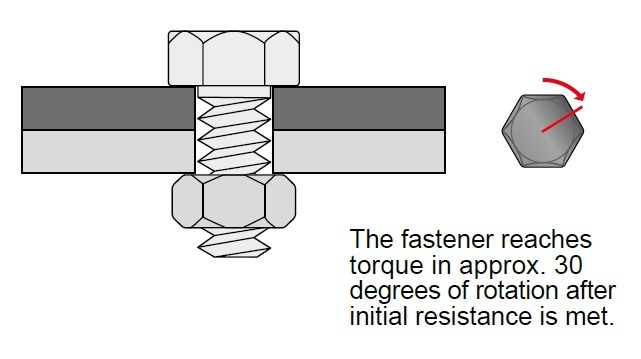
A hard joint has has low resistance when turning the bolt or nut until it reaches its seating, after which resistance rapidly increases. A hard joint occurs where the material between the nut and has a high stiffness when subjected to compression by the bolt load. A metal to metal joint results in a hard joint.
< Back to resources